System integration: the next strategic advancement in pharma manufacturing
Pharmaceutical manufacturing is expected to enter, in the next few years, in a pivotal era, defined by a great digital transformation. System integration is the cornerstone of this process, oriented to three fundamental goals: compliance, to meet stricter regulations; quality, to ensure product integrity and patient safety; efficiency, to optimize production times and costs.
In this article we will discover the key trends that are actively shaping pharma manufacturing, while gaining deeper insights into the evolving regulatory landscape and analyzing data-driven metrics. Join us in this journey through the challenges and opportunities offered by system integration.
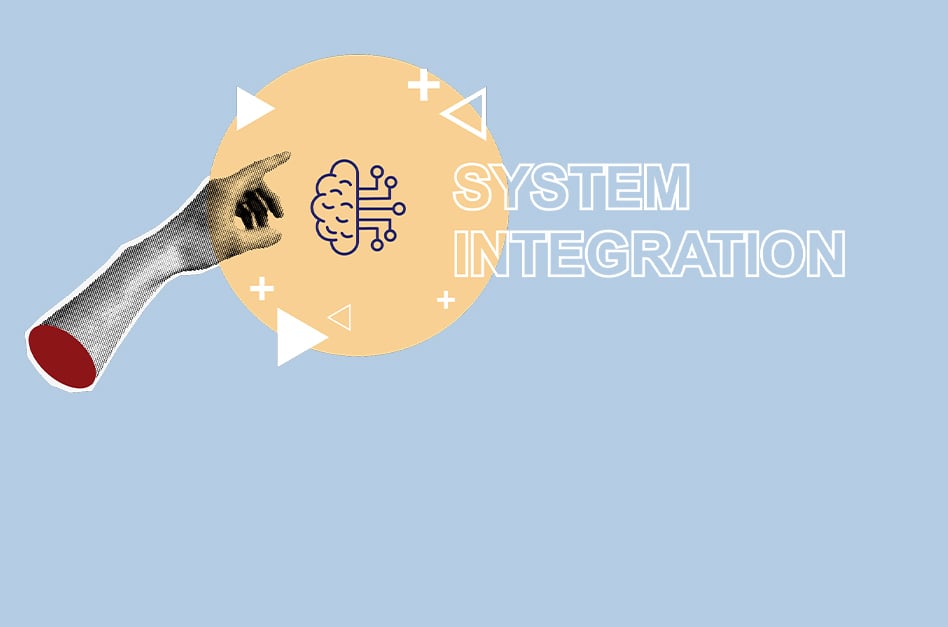
The three main trends that are shaping pharma industry
Pharmaceutical manufacturing is set to experience significant advancements over the next five years, as new trends in medicine are driving the need for system integration.
Starting with personalized medicine production, which tailors treatments to individual patients, often occurring in limited, customized batches. Integrated systems will play a crucial role in ensuring the agility required for this level of patient-specific treatments, making real-time adaptability of production processes a key competitive advantage.
Companies are also leveraging SCADA (Supervisory Control and Data Acquisition) and historian systems to create digital replicas of manufacturing environments. This innovative approach is a powerful tool for process optimization, allowing manufacturers to simulate changes and predict their outcomes to enhance efficiency of the production.
Predictability is also crucial for better machine maintenance. By analyzing time-series data from historian systems, companies are moving beyond scheduled check-ups towards predictive maintenance models, resulting in minimized shutdowns and extended equipment lifecycle.
Digitalization: a pivotal transformation in manufacturing
The discussion on system integration is no longer just a matter of technical convenience, but a strategic necessity. Softwares like SCADA and MES (Manufacturing Execution Systems) are being integrated with historian systems, leading to deep transformations in the way companies operate. Through real-time monitoring and analysis of key metrics, integrated systems provide valuable insights, empowering decision-makers to respond more precisely to production demands.
A well-executed digitalization is not only key to transforming biopharmaceutical supply chain processes, but it is also essential to ensure regulatory compliance and patient safety while fulfilling sustainability goals. Companies willing to invest now in system integration will then hold an advantaged position over the others, achieving faster production times, lower operational costs and, ultimately, higher profits.
Seamless integration, the driving force for regulatory evolution
At the heart of the system integration process lies a critical driver, regulatory evolution, which is prioritizing data integrity, traceability and real-time monitoring.
Guidelines such as FDA’s 21 CFR Part 11 and EMA’s Annex 11 continue to expand, demanding robust systems for electronic records and signatures. The emphasis for these frameworks has shifted towards seamless communication between production equipment and higher-level systems like SCADA and MES, driving the demand for smart equipment.
At the same time, regulatory bodies are actively promoting continuous manufacturing, which necessitates a seamless integration of SCADA and MES systems to monitor Critical Quality Attributes (CQAs) and Critical Process Parameters (CPPs) in real-time. Data exchange between equipment and SCADA systems is essential to maintain production consistency while meeting stringent quality requirements. Continuous data logging and advanced visualization tools allow manufacturers to detect even the slightest deviations and take immediate corrective action.
As expectations for system integration grow, secure communication protocols between equipment and SCADA/MES systems are becoming a critical priority. Cybersecurity measures, such as data encryption and secure network architectures, are crucial to defend sensitive production data and prevent disruptions in operations.
The measurable impact of integration
The impact of system integration in pharmaceutical manufacturing is not theoretical, but measurable with reports and benchmarks: the benefits are concrete.
According to McKinsey, facilities that integrated MES with historian systems are experiencing batch release times up to 30% faster, leveraging automated review-by-exception processes.
Deloitte reports show a 20% reduction in compliance deviations and a 15% integration in Overall Equipment Effectiveness (OEE) in companies with end-to-end integrated systems. As of today, over 70% of pharmaceutical manufacturers consider system integration among their top three strategic priorities for operational excellence. For many, it has become the foundation for smarter decision-making, streamlined compliance, and long-term competitiveness.
Overcoming challenges with smart solutions
While the benefits of integration are well established, companies still need to overcome many challenges in order to reach a successful adoption.
The first obstacle is financial. The capital expenditure (CAPEX) required for system integration is very high and remains a barrier for many facilities. However, cloud-based MES platforms are addressing this issue by offering scalable, modular solutions with lower upfront costs.
Another common challenge is the effective and seamless integration between process equipment, Human-Machine Interfaces (HMIs), and SCADA systems. PLC- and PC-based architectures, leveraging standardized communication protocols like OPC UA, are beginning to bridge the gap by ensuring real-time data exchange, reduced latency and secure data flows.
Lastly, fragmented data systems limit real-time insights and process optimization. The industry is responding with centralized historian systems and API-driven architectures, increasingly adopted to enable seamless data flow across legacy equipment.
The transformative potential of system integration
System integration in pharmaceutical manufacturing has evolved from an option to a strategic necessity for compliance, quality, and efficiency. Beyond these well-known benefits, emerging trends and real-world applications highlight its transformative potential in tackling industry challenges and securing long-term success. By embracing these insights and strategies, pharmaceutical manufacturers are enabled to faster decision-making to stay one step ahead in an ever-evolving landscape.