The invisible battle of sterilization: safeguarding pre-filled syringe integrity and patient safety
What looks simple is often the most complex. Pre-Filled Syringes (PFS) are a modern solution in drug delivery, but behind their convenience lies a critical challenge: sterility. This article uncovers the hidden risks and technical demands of PFS sterilization, following the invisible battle between pressure, temperature, and product integrity. Discover how advanced methods are redefining safety, one syringe at a time.
In the ever-evolving pharmaceutical industry, few innovations seem as straightforward, and yet are as deceptively complex, as Pre-Filled Syringes (PFS). Convenient, accurate, and ready to use, PFS products represent a leap forward in drug delivery. But behind every perfectly sealed syringe lies a silent, high-stakes challenge: integrity and sterility.
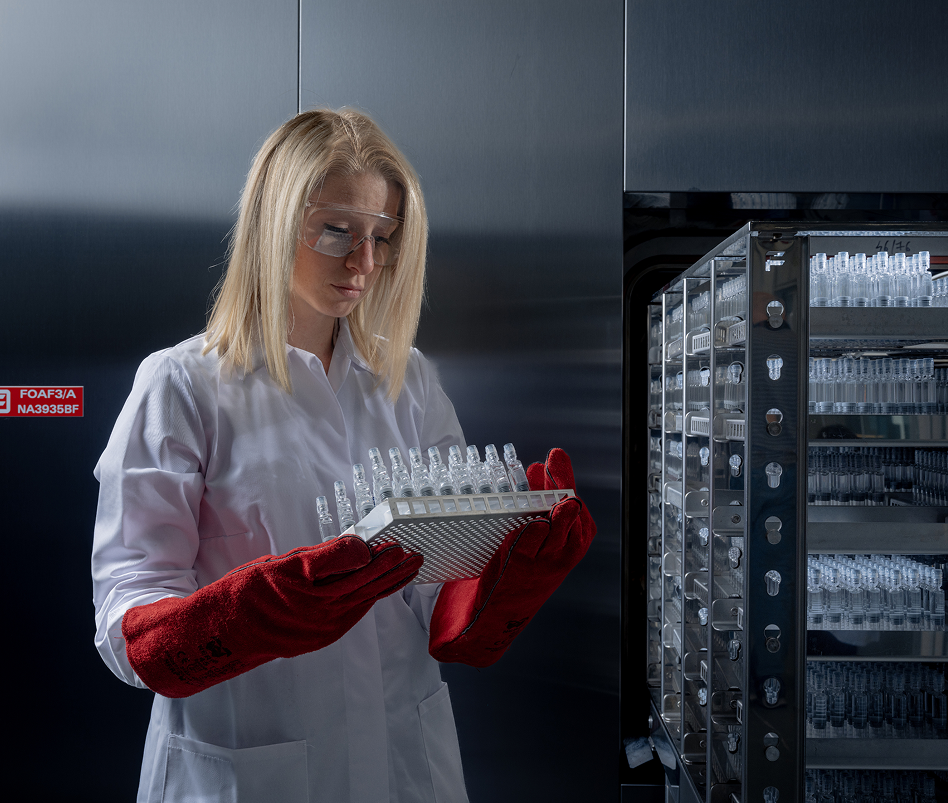
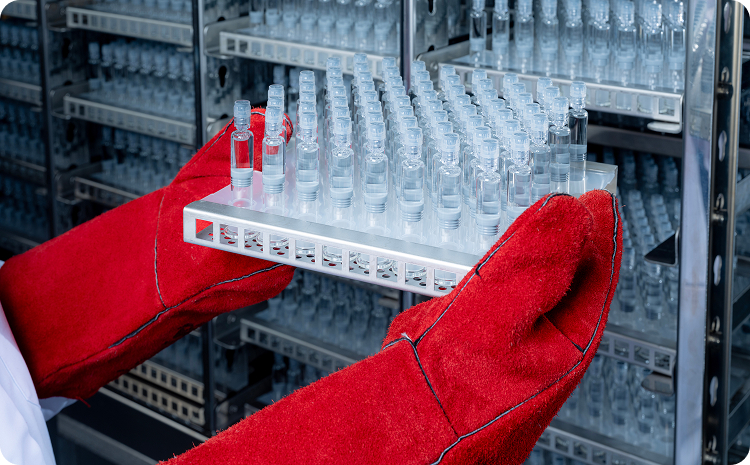
Behind the simplicity,
a complex threat
Pre-Filled Syringes are hermetically sealed containers filled with injectable solution, a movable plunger, and a cap. Their design suggests ease and reliability. But the sterilization of these devices is anything but simple.
When heated, the solution inside the syringe expands, causing a surge in internal pressure. Without precise control, this internal pressure can force the plunger outwards, potentially leading to water entrainment in plunger grooves or even plunger expulsion, directly compromising the product's sterility and functionality. Such failures threaten both product efficacy and patient safety, making PFS sterilization a uniquely delicate and demanding process, far beyond the scope of traditional sterilization methods.
Why traditional autoclaves fall short
Most conventional autoclaves, especially pure steam systems, were never designed to address the specific needs of PFS sterilization. In these systems, temperature and pressure rise in a fixed relationship, meaning pressure cannot be adjusted independently to offset the internal conditions of the syringe.
This creates a dangerous scenario: the internal pressure of the PFS exceeds the external chamber pressure, resulting in risks like forcing out the rubber plunger movement, drug loss, or incomplete sterilization.
Such issues can lead to serious regulatory non-compliance, reinforcing the need for specialized sterilization methods tailored to the unique behavior of pre-filled devices.
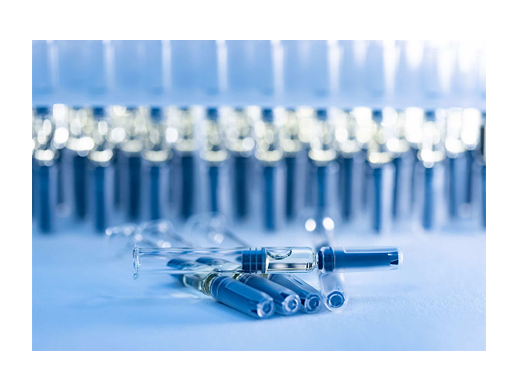
The key to success: pressure and temperature management
Sterilizing pre-filled syringes is not just about microbial inactivation, it is about doing so without damaging the product.
Success depends on a customized cycle that carefully balances two key variables: the thermal sensitivity of the drug solution and the structural characteristics of the syringe.
The process involves multiple phases: it begins with a gradual pressure increase during the heating stage, maintains a balanced pressure during exposure, and applies overpressure during cooling to return the plunger to its original position.
This precise approach ensures effective sterilization while preserving the chemical and physical integrity of the product.
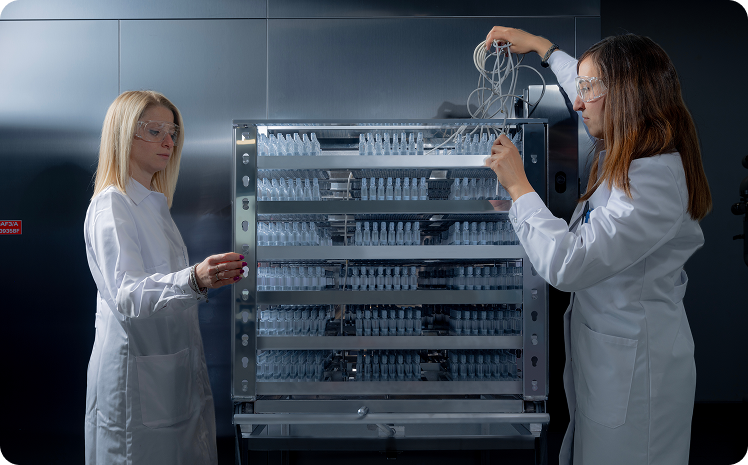
Advanced Solutions
To overcome the inherent challenges of PFS sterilization, a more advanced solution is required. Our FOA technology represents the answer to the limitation of traditional systems, indipendently governing the chamber pressure throughout the entire cycle and precisely equilibrating the pressure inside the sealed PFS. This technology creates a unique sterilization environment where chamber pressure remains closely aligned with the internal pressure of the PFS throughout the cycle. The result: effective microbial inactivation (SAL achieved), with the added benefit of maintaining the essential quality attributes of both the container and the drug product.
This solution prevents thermal degradation and mechanical damage, both of which could otherwise compromise product safety and efficacy.
Looking ahead: a safer future, one syringe at a time
Sterilizing pre-filled syringes is a highly complex process that requires precision, expertise, and innovation. The intricate balance between temperature, pressure, and material integrity demands solutions that go beyond standard equipment.
By embracing advanced equipment and designing carefully controlled sterilization cycles, the industry can meet and exceed the highest standards of sterility and compliance.